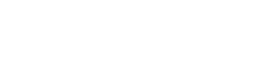
If subsea electronics are maintained at atmospheric pressure, many commercially-available devices can be used without modification. However, the cost, size, and weight of pressure vessels all become increasingly significant as the depth rating is increased. By contrast, use of pressure-tolerant electronic (PTE) systems - designed to operate in fluid-filled enclosures at the ambient ocean pressure - eliminates high-pressure interfaces. Flooding and implosion risks are mitigated, electrical and optical connector/penetrator requirements are simplified, and the inspection and maintenance burden is reduced.
Of course, there are also drawbacks to this technology: the range of commercially-available PTE systems is comparatively small, and development and qualification procedures are more complicated than those for ordinary atmospheric pressure systems. Pressure-cycling also causes mechanical stress which inevitably reduces component lifetimes. Nonetheless, PTE systems remain attractive for many subsea vehicle and long-term deployed equipment applications.
Some PTE systems with depth ratings of up to 6000m are relatively common, frequently commercialized for the oil and gas industry. Although the principles and techniques for designing greater depth-rated pressure-tolerant electronics are the same, there are few such commercially-available systems because the application scope is very small.
Though the costs and risks associated with development of PTE systems are undeniably greater than those associated with developing their atmospheric pressure counterparts, they are frequently smaller than imagined. Component qualification and pressure testing does extend the development timeline, but with experience, the behaviour of individual components under pressure is often predictable.
This paper focuses on the design of low-voltage (up to 600V) and low-power (up to 10kW) pressure-tolerant electronic systems, which are becoming common for manned submersibles and unmanned robots designed to explore the deep ocean trenches.
Before attempting any pressure-tolerant electronics (PTE) system development, an important first step is determining whether the benefits of this technology outweigh the drawbacks for a particular application, and whether the overall approach is appropriate for the clients' risk tolerance, development timeline, and other constraints.
When a PTE system is being considered, and no commercial-off-the-shelf (COTS) system is available, one of two approaches may be taken: modification of an analogous one-atmosphere system for high-pressure operation, or development of a pressure-tolerant system from the electronic component level. The preferred approach depends on the cost and specialty of any analogous one-atmosphere systems, the likelihood of successful modification, the design elegance of the modification, the reliability requirement of the application, and economies of scale in production. The degree of testing is primarily influenced by the clients' development timeline. There is a trade-off between developing empirical knowledge which will lead to surety of long-term performance, and rapid turnaround of designs required for short-term projects.
The lowest-cost approach is normally to start with one-atmosphere COTS equipment and replace crystal oscillators, electrolytic capacitors, and other known-incompatible components with pressure-tolerant equivalents, and then test the modified equipment in a pressure chamber. Most commercial products are "black-boxed" from the end user perspective, so if the modified equipment doesn't meet the necessary specification, then it may be impossible to diagnose the problem. At this point in the process, it is usually more practical to develop a new PTE system from the electronic component level. Though few components are designed or intended for operation in high ambient pressure environments, many are inherently pressure-tolerant, or can be made so through potting (reinforcing the structure to support internal void spaces) or porting (drilling to allow internal void spaces to fill with fluid).
The component-level development approach is more time consuming than modifying existing equipment, but it gives complete control over the design, enabling it to be optimized for the application. For example, in switch mode power supply (SMPS) design, to achieve given power handling and conversion efficiency, capacitance and inductance requirements may be traded-off to some degree. COTS power supples are frequently optimized for low inductance, as this is the lowest-cost approach. However, for pressure-tolerant applications, where bulk capacitance is generally more difficult and expensive to implement than bulk inductance, a different topology which favors lower capacitance might be preferable. Developing PTE systems from the electronic component level also results in design ownership, longer-term parts availability, lower costs of production, and enables any pressure-related problems to be diagnosed at the lowest applicable level without reverse-engineering.
Hydrostatic pressure affects different types of components in different ways, depending on their construction, packaging, and operating principles. Though the concept of designing electronic systems to operate in this environment is initially daunting, success rates can be high even without extensive performance characterization and testing of individual components. In some cases, with experience and a thorough understanding of the component selection and design techniques described here, it's possible to produce successful designs without testing individual components at all.
When discussing component-level development of pressure-tolerant electronics, one question I am often asked is: "do you have a list of qualified components?" Although the bill-of-materials for any previous successful pressure-tolerant design could be considered a list of qualified components, in reality the situation is not so black-and-white. In certain specific cases, such as transistors or quartz crystals in metal cans, pronounced mechanical failures can be expected, making it easy to determine a statistical crush pressure with a confidence interval. However, the failure modes of most practical components are much more subtle and difficult to quantify. To select components with a reasonable chance of success, an understanding of material properties and manufacturing methods is required.
In qualifying a component, the first step is to define a procedure - perhaps pressure-cycling to a specific pressure and back to atmosphere a number of times, with controlled ascent/descent rates and hold times. Then it is necessary to define a pass level - perhaps in terms of component value change, transfer efficiency, or frequency performance. The required pass level might vary between applications, or even between different ways of using the same component in the same application. Now consider that major electronic component distributors routinely stock (and designers routinely choose from) literally millions of different part numbers, which means that any individually-maintained white-list would be both hugely restrictive and quickly outdated. This is why I don't maintain a list of specifically qualified components, instead providing high-level guidance to aid in selecting likely candidates from the entire range of available components.
Here are introduced several different testing methodologies which have been adopted for component, module, and production design testing. When testing new or unknown components, initial testing need not involve any electrical context at all. Simply pressure-cycling components and watching, listening, or later examining them for physical damage may provide enough information to indicate likely failure modes or to disqualify a part. But ultimately, cycle testing of production designs is required to ensure long-term reliability in the final application.
In this technique, the component or module is loaded into the pressure chamber, then gradually cycled to the test pressure and then back to ambient pressure. This is often the first step in testing a new or unknown component. This technique can identify problems with sealed components and even encapsulated assemblies. For example, passive testing of a fully-encapsulated DC-DC converter revealed a sealed bimetal over-temperature cutout switch that collapsed with moderate pressure.
An extension of the passive testing concept is absorption testing, where a component is gradually pressurized, then held at the test pressure for a specified time, and then rapidly depressurized. This process deliberately exacerbates mechanical problems and tends to explode parts that absorbed fluid during the pressurization step, which might not be noticed during a gradual depressurization. Void spaces which collapse can usually be identified by passive testing, and absorption testing can identify void spaces which flooded instead.
For performance-critical components, or those which are expected to be sensitive to pressure, designing a test circuit to measure the performance of the part under pressure may be necessary. This step can save time by identifying problems with components before they're used in a complex design. Examples of this process include transistor curve tracing or opto-isolator CTR measurement. One technique for automated testing of passive components is to switch them to form RC timing circuits, measured against reference components outside the pressure chamber. This technique can quickly quantify value dependence with pressure for a wide range of component types and values.
Cycle testing implies repeated pressurization and depressurization with defined rates, endpoints and hold times. Characterising components during cycle testing is part of a methodical approach necessary to quantify the effects of pressure over time, in much the same way as accelerated MTBF testing is performed using environmental chambers. When the component packaging does not support the full test pressure, mechanical stresses are transmitted to internal parts, and repeated pressure-cycling can lead to performance degradation over time. If the project scope permits it, then cycle testing may be applied to individual components, otheriwse it's typically reserved for production designs as whole assemblies.
Though most electronic designers are familiar with a range of available components, few have the necessary knowledge of materials and manufacturing methods to understand why particular types of components are more suitable for pressure-tolerant operation than others. Development of PTE adds aspects of materials science research on top of the typical engineering development process. This section provides general advice for selecting parts for component-level pressure-tolerant designs. Using this guidance rather than relying on a white-list of pre-qualified components enables greater design flexibility through the use of new components.
Most surface-mount resistors (thick and thin film types), as well as most carbon and metal film axial types are void-free and suitable for high-pressure use. All types will exhibit some change in value with pressure, as the resistive element physically shrinks in size. Due to the nature of their construction, thin film types exhibit less value/pressure dependance than thick film types. High-power wire-wound resistors of various constructions have also been used with success. In fact, the relatively higher thermal conductivity of many fluids increases the power dissipation capability of these parts relative to their use in free air.
The resistance of classic carbon composition resistors (rarely used in modern electronics) does vary significantly with pressure, as the carbon particles are compressed to form a denser resistive element, making them a good example of a component generally unsuitable for use in pressure-tolerant applications.
Aluminium electrolytic capacitors are by far the most cost-effective and widely-used type where moderate-to-large capacitances are required. However, their wound construction includes small internal air spaces, which causes them to deform, leading to electrode short-circuits when exposed to high ambient pressure. Puncturing the case can alleviate this effect, but then the electrolyte is displaced by the dielectric fluid over time. Existing designs using aluminium electrolytic capacitors can often be adapted for pressure-tolerant operation by replacing these capacitors with ceramic types, and adding additional series resistance to match the ESR if necessary.
Injection-molded polymer film capacitors are generally void-free and relatively unaffected by high ambient pressure (though dipped types are often not). Solid tantalum capacitors are also acceptable candidates, though recent advances in ceramic capacitor technology have superseded solid tantalum capacitors in most applications.
The huge compressive strength of ceramic capacitors results in low value/pressure dependence and long lifetimes in pressure-tolerant applications. However, their brittle nature makes surface-mount types subject to fracturing, due to differential shrinkage effects between the capacitor and the circuit board. Where physically large capacitors are required, types with soft terminations intended primarily for automotive and other high-vibration environments are a good choice. Ceramic capacitor arrays with spot-welded J-leads also add a degree of flexibility and compliance between the capacitor and the circuit board. Examples of ceramic capacitor arrays with J-leads are visible in the adjacent power switch figure.
Some effects of hydrostatic pressure on magnetic materials, especially ferrite, have been documented. However, these effects are neglible in the context of ordinary power system designs. We have successfully tested a number of shielded and unshielded ferrite core inductors and transformers. Potted types often contained air spaces which flooded during the initial pressurization, and small inter-winding gaps and air pockets are of little concern.
Traditional oscillators based on mechanical resonators include quartz crystals, MEMS, and SAW resonator types. Until very recently, there has been no practical pressure-tolerant alternative to any of these devices. Because fluid-filling would dampen mechanical oscillations, an air space must be maintained, so two techniques are commonly used: the component is potted in a rigid encapsulant, or a miniature pressure vessel is formed.
In the last few years, a new type of silicon oscillator based on a tunable on-chip LC filter has become available. This device is constructed using conventional CMOS manufacturing processes and operates without mechanical resonators, so no air space is required.
Classical opto-couplers maintain a small air space or an index-matching gel between the photoemitter and the photodetector. Depending on the construction of the package, external pressure can deform it, crushing this volume and attenuating the signal. For phototransistor-output isolators, it is possible to measure the current transfer ratio, which can quantify a degree of pressure tolerance, but for digital isolators, this is impossible.
Relatively recent developments have led to on-chip magnetically and inductively-coupled isolators, which are typically constructed without any voids. These types of isolators appear to be a good choice for pressure-tolerant applications.
Until recently, high intensity discharge (HID) arc lamps have offered the best combination of luminous efficiency and spectral output for both human and camera visualization. But light emitting diode (LED) technology has been rapidly improving, both in terms of luminous efficiency and available spectral output, and it has displaced HID in most subsea applications.
Like most other semiconductor devices, LEDs themselves are inherently pressure-tolerant, and circuit board indicator style LEDs can be used in fluid-filled environments without issue.
However, differential shrinkage can cause problems with wire bonds in large LED arrays, and polymeric encapsulants have been known to locally oxygenate or otherwise interact with dielectric fluids, leading to "browning". For these reasons, most commercially-available subsea LED lights still maintain a one-atmosphere volume for the LED elements.
We have measured the linear compression characteristics of conventional epoxy-packaged integrated circuits (ICs) in the high hydrostatic pressure environment, and they are similar to those of FR4 fiberglass circuit board material, so we expect that pressure-induced forces on solder joints are small. Leaded packages provide an additional degree of compliance between the part and the board, which may contribute to increased reliability and longevity.
Many modern parts are only available in smaller ball grid array (BGA) or dual/quad flat no-leads (DFN, QFN) and similar packages. Though we have had initial success testing some of these packages, we do not have sufficient data from which to draw a firm conclusion on their long-term reliability.
Parts with hermetically sealed packages such as CERDIP, LS8 and similar contain a significant air volume and are expected to crush at low pressures. These parts may be carefully drilled to enable fluid-filling, though the dielectric properties of the fluid need to be considered when in direct contact with the die in this way.
Perhaps of greater concern than the board/part interface are effects on the die and wire bond connections internal to the package. High compressive forces are transmitted through the package, and the die shrinks as a result. Though the process thresholds used in CMOS ICs appear to be large enough that CMOS operation is generally unaffected, the accuracy of analog components such as voltage references and op-amps is measurably degraded.
Designers of high-precision analog circuits have used various techniques to deal with thermal die-stress induced effects, and the same principles apply to the die-stress effects induced by high hydrostatic pressure. Techniques include regular re-calibration or self-calibration to account for pressure effects, as well as strategic IC and circuit board cutout placement. The highest precision applications almost certainly require a small one-atmosphere volume.
Most power silicon devices we have tested have worked without issue, however, we suspect that larger die areas and higher-current terminal bonding methods are more susceptible to pressure cycling effects, so we have avoided using devices with large die areas or highly-integrated packages, using arrays of smaller devices wherever possible.
For low-voltage switching, MOSFET devices have a temperature characteristic which tends towards equal current sharing, so parallel arrays can be used effectively. For higher-power and higher-voltage switching applications, bipolar-type devices are typically used. R. Pittini and M. Hernes "Pressure-tolerant power electronics for deep and ultradeep water", referenced at the end of this report, includes a discussion of modifying commercially-available high-power IGBT modules for long-term pressure-tolerant operation with good results.
Classical wire fuses, and their glass-, plastic-, and ceramic-bodied counterparts can be ported, allowing them to be fluid-filled for use in high pressure environments. However, they are subject to an obvious problem: fluids have a much higher heat transfer coefficient than air, which effectively increases the fuse rating. Further, the fusible element tends not to vaporize as designed, instead it encourages a plasma channel to form through the fluid. Self-resetting PTC-type fuses have a different problem: the pressure physically compresses the fusible element, preventing it from expanding and separating the conductive particles inside.
In general, the use of one-time and self-resetting fuses can be avoided in pressure-tolerant electronic designs, replacing this functionality with electronic current limiting. There are still specific instances where one-time fuses are appropriate, and the most common solution is to use solid-encapsulated type fuses, or encapsulating ordiary fuse wire in a polymer injection mold or syntactic foam.
Pressure-tolerant battery systems are of particular interest for untethered and fiber-tethered underwater vehicle designers, because a significant proportion of the vehicle mass is typically attributed to batteries. If the batteries are contained in a pressure vessel, the dry weight manifests as negative buoyancy, whilst if they are pressure-balanced instead, they displace their own volume of water and the effective buoyancy can be almost neutral.
Most rectangular prismatic and cylindrical-wound cells have small internal air spaces which cannot easily be filled or ported, and which render them unsuitable for high-pressure operation. However, lithium-polymer pouch-type cells are vacuum sealed as part of the manufacturing process, which eliminates most air spaces. Not all pouch-types cells are suitable for use in high pressure environments - we have discovered subtle differences in cell construction which affect the reliability, however one known suitable cell is described by K. Rutherford and D. Doerffel in "Performance of lithium-polymer cells at high hydrostatic pressure", referenced at the end of this report.
In general, brushed motors should be avoided because the commutator performance is degraded in the presence of fluids, but it is common practice to fluid-fill hybrid stepper, DC brushless, and AC synchronous motors for sub-sea applications. Commonly, conductive cooling through the fluid increases the power handling capability many times relative to the air-cooled rating. However, depending on the internal construction, the operating speed, and the fluid used, viscous losses may also be very high.
In our experience, high-performance ironless motors with very high copper fill factors and small running clearances were more susceptible to overheating than their conventionally-wound toothed-stator equivalents. I expect this is a result of high viscous losses due to the large shear surface area, and the relatively small contained fluid volume, but this has not been deeply investigated.
For propulsion applications, we have had the greatest success with brushless DC motors. "Outrunner" type construction leads to high pole counts, easing winding requirements to achieve lower voltage/speed constants required for direct-drive of propellers in water. Because there is no mechanical commutator and no exposed connections, this type of motor can be epoxy-dipped or vacuum-potted for short-term use in seawater. For longer-term applications, materials compatibility will likely dictate installing the motor in an oil-filled housing.
Following are some selected papers relevant to the design of pressure-tolerant electronic subsea vehicles and deployed-equipment applications.
A canonical early review paper published by the U.S. Navy:
H. E. Barnes and J. J. Gennari, "A review of pressure-tolerant electronics (PTE)"
Naval Research Laboratory, Washington DC, June 1976
Operation of Lithium-polymer pouch cells at 60 MPa:
K. Rutherford and D. Doerffel, "Performance of lithium-polymer cells at high hydrostatic pressure"
Proceedings of the 14th Intl. Symp. on Unmanned Untethered Submersible Technology, 2004
Bluefin Robotics first and second generation batteries:
R. Wilson and S. Somlyody, "Pressure-tolerant lithium polymer batteries"
Sea Technology, April 2009
On quartz crystals, silicon oscillators, and a PTE camera:
P. Kampmann, J. Lemburg, H. Hanff and F. Kirchner, "Hybrid pressure-tolerant electronics"
Oceans, pp. 1-5, October 2012
Porting of high-power IGBT bricks for power conversion:
R. Pittini and M. Hernes, "Pressure-tolerant power electronics for deep and ultradeep water"
Oil and Gas Facilities, pp. 47-52, February 2012
Nic Bingham leads practical R&D spanning many disciplines, specializing in electronic systems for extreme environments. He has spent months at sea supporting ambient-pressure electronics in the deepest trenches of the world ocean, and conducted three missions to service autonomous solar-diesel power plants operating on the high domes of the Antarctic plateau.
He has designed a wide range of pressure-tolerant systems for ROV, AUV, and HOV applications. Most recently, he designed the power distribution systems and vehicle control networks for the Deepsea Challenger submersible, as well as the unique pressure-tolerant motor controller used to drive all its thrusters and hydraulic pumps.
As an engineering manager, a laboratory supervisor, a student mentor, and the inventor and author of several Australian and U.S. patents, he has walked the fine line between industry and academia for many years. He is also an advocate for science education and resource conservation, believing these two areas to be closely linked.
(C) 2013 Unmanned Underwater Technology